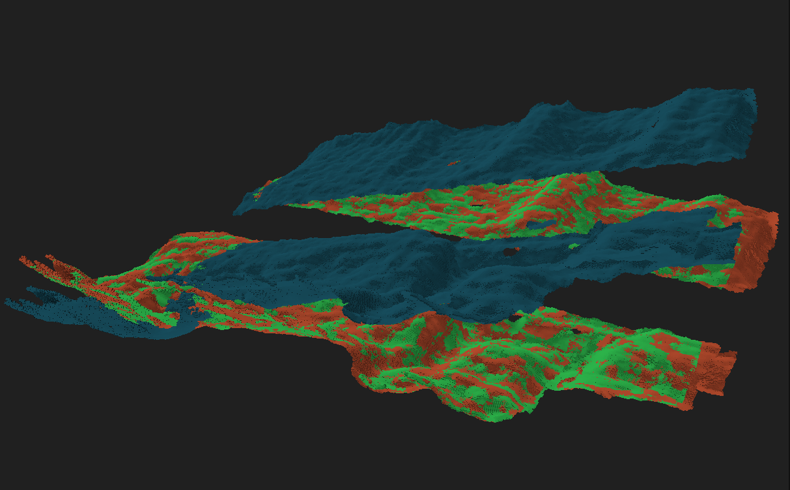
Manufacturing prioritizes cost savings and efficiency. To optimize automation processes, understanding the tools that provide the best value is crucial for reducing downtime and improving throughput.
What is Cycle Time and Why is it Important?
Process cycle time, the duration from start to end of a single process, is a key performance indicator (KPI) in automated process design. It encompasses time spent on work, wait time, value-added time, and non-value-added time.
Throughput, another KPI, is inversely related to cycle time. Reducing process cycle time is vital for increasing throughput, a key component in optimizing manufacturing efficiency and reducing the cost per unit manufactured.
Understanding cycle time is the initial step in evaluating components within automation processes that enhance overall efficiency.
Inferred 3D Vision Guidance
In contrast to True 3D, inferred 3D machine vision systems usually require specific conditions.
The first condition is dedicated lighting to control the visual environment. Inferred 3D vision systems rely on consistent feature contrast for imaging and accurate positional information calculation. While this may not initially appear to impact process cycle time or throughput, it can affect these metrics over time. System-specific lighting is a common component of inferred 3D vision systems, potentially causing downtime and requiring upkeep.
The second condition is that inferred 3D systems rely on 2D features to measure the 3D position of an object. Imaging features on a medium to large part often requires multiple images, impacting cycle time during the multi-imaging process.
These image capture methods tangibly impact cycle time derived from inferred 3D vision system reliance on datum or known features.
Volumetric “True 3D” Machine Guidance
In contrast to these conditions, 3D vision guidance systems use volumetric sensors to map the part’s surface. This “true” 3D vision calculates positional information using 3D images without structured light, multiple image captures, or profile scans. Volumetric sensors have a wide field of view, a small device footprint, and the ability to view the part from various distances, including an angled view.
Utilizing volumetric 3D vision guidance reduces cycle time by eliminating the need for structured lighting and multi-point measurement or profile scans, optimizing automation, improving throughput, and reducing downtime.
Liberty Robotics Vision Guidance – Case Study
Challenge
Liberty Robotics conducted a cycle time reduction study with a partner, comparing an inferred 3D vision guidance system to volumetric 3D vision guidance in an automotive cosmetic hem sealing application.
Solution
The inferred 3D vision guidance system took 3 measurements from three different points to triangulate the door’s location based on positionally known (datum) features. It took 11 seconds to drive the robot to different locations and capture images. The sealer application took an additional 24.8 seconds, resulting in a total cycle time of approximately 36 seconds.
In contrast, the V-Guide™ 3D volumetric vision system took a single measurement to capture the door’s position. The robot movement and image capture time totaled 2.9 seconds. The improved rotational accuracy allowed Liberty Robotics’ partner to increase the speed of the sealer application, reducing the cycle time from 24.8 to 19.1 seconds. On average, the total cycle time for the application using volumetric 3D vision guidance was 22 seconds.
Results
A net savings of 13.9 seconds by improving the robotic vision guidance system had significant ramifications in overall efficiency and throughput. Despite the cost of installing multiple 3D vision systems, the partner saw a return on investment in under a day (18 hours).
3D Volumetric Vision Guidance Benefit Summary
- Efficiency Improvement: Volumetric 3D vision guidance eliminates the need for structured lighting and multi-point measurement, streamlining the automation process.
- Cycle Time Reduction: Significantly reduces cycle time by providing accurate positional information with a single measurement, allowing for faster and more precise robotic movements.
- Throughput Enhancement: Improves throughput as the reduction in cycle time leads to increased operational speed and efficiency.
- Maintenance Optimization: Minimizes downtime and maintenance requirements compared to inferred 3D vision systems, which may rely on structured lighting and multiple scans.
- Cost Savings: Offers a cost-effective solution by eliminating the need for additional components like structured lighting and reducing overall operational time.
- High-Accuracy Rotational Information: Generates a comprehensive surface map, providing high-accuracy rotational information in six degrees of freedom without relying on datum or known features.
- Real-world Application Success: Demonstrated success in an automotive cosmetic hem sealing application, showcasing a substantial reduction in cycle time and immediate return on investment.
Contact us today for a virtual or in-person demo to experience the transformative power of volumetric 3D vision guidance in your manufacturing processes. Stay up to date with products and information by following us on LinkedIn.