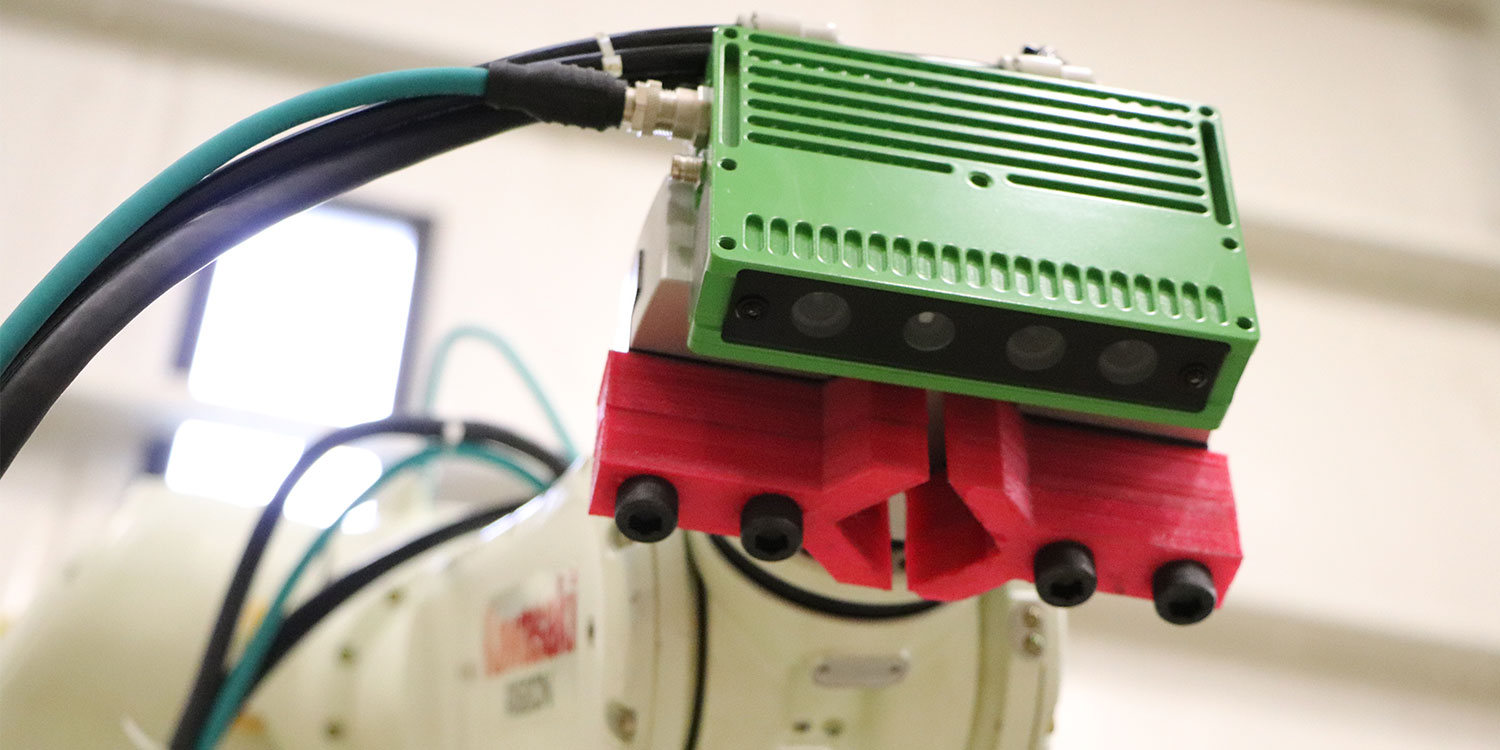
Machine vision is quickly becoming a necessity for many manufacturers looking to cut automation cost and increase production. Industrial robots are optimized by essentially giving them sight, which allows them to perform more dangerous and repetitive tasks efficiently. With production output demands increasing, automation technology is a necessary ally. Traditional machine vision is not foolproof, but Liberty Reach has already overcome one of the biggest nuisances of robotic vision systems: their need for lights. Here are 3 reasons you will want a system that does not require a light:
1. You won’t waste time on finding the correct light.
Traditional machine vision camera optics require a light source in order to take an usable image. Picking the correct light is essential for producing consistent results. The range of machine vision applications can vary, which requires careful consideration of the geometry (light direction), color (spectrum), structure (light pattern), and filtering of the light in order to pick the appropriate light source.
Light sources can be fluorescent, quartz halogen, LED, metal halide, or xenon. The angle and diffusion of each light is also important to take into account. Each system has to be meticulously configured in order to function properly in the robot cell which adds extra time and effort when setting up a system.
2. You won’t need to worry about ambient light.
Factory conditions are unpredictable and light conditions are rarely constant. Without proper testing, the ambient light changes can cause system malfunctions. There are many different sources of ambient light to consider, including overhead lights, task lights, sunlight, indication lights, and other vision system lights. You then have to think about how to properly block these sources from interfering, which can involve covering the source, counteracting the ambient source with a strong strobe, turning off the source if possible, or using a variety of camera filters. Again, taking up more time and resources.
3. You’ll save money and add value.
Not only does each robotic vision sensor require a light, but also the accessories and hardware that come with it. A four-sensor camera system requires proper mounting, filters, and cables, which average around $4,000. Adding shutters and pneumatics can nearly triple that cost.
Liberty Reach sensors do not rely on constant lighting conditions or an external light source. Eliminating external lighting reduces production interruptions and support costs. Liberty Reach systems use 3D images to calculate the position and orientation of a body reliably, even in an evolving plant environment.
Eliminate the need for machine vision lights by switching to a system that can operate in the dark. To see the system firsthand, sign up for a free virtual or in-person demo.